Alle Angaben sind Richtwerte ohne Gewähr.
Infos und Lösungen für Ihren optimalen Werkzeugeinsatz
Generell zu beachten
- Vorwiegend Gleichlauffräsen
- Vollspur (=ae 100% bzw. 1 x D) vermeiden nur als Ausnahme
- Große Umschlingung des Fräsers vermeiden
- Fräser R immer kleiner wählen als Kontur R (Innenkontur R4 Fräser R max. 3,5)
- Eckkonturfräsen Innen = Vorschub (Vf) absenken (50%)
- Senkrechtes Eintauchen vermeiden da sonst großer Fräser Verschleiß und Ausbruchgefahr
- Eventuell Prozessumstellung auf Bohren und danach Fräsen
- Geeignetes Fräsmaschinenkonzept inkl. Programmiersystem stabile dynamische Maschine mit genauem Rundlauf und schneller Steuerung
- Gleichmäßige Schlichtoberfläche entsteht wenn: fz = ap = ae = Schlichtaufmaß
- Vorschub pro Zahn fz immer einhalten wenn der errechnete Vf aufgrund Kontur/Fräsweg unerreichbar ist Drehzahl senken
- wenn errechnete n (Drehzahl) aufgrund maximaler Spindeldrehzahl unerreichbar ist Vf senken
- Tischvorschub Vf so abstimmen, dass Maschine dynamisch und gleichmäßig fahren kann, Ruckartige Bewegung vermeiden.
Tipps zur Kühlung
- Immer zur Schnittzone richten, Unterbrechnungen vermeiden
- Beim Hartfräsen vorwiegend mit Luft kühlen
- Emulsion mind. 7%
Richtiger Einsatz der Spanntechnik
- Spannmitel zur Bearbeitung wählen z.B. Schruppen > Kraftspannfutter / Weldonfutter, Schlichten im kleinen Durchmesserbereich > Schrumpfen
- Sauberkeit
- Auf Rundlauf achten, eventuell mit Messuhr einmessen
Richtwerte
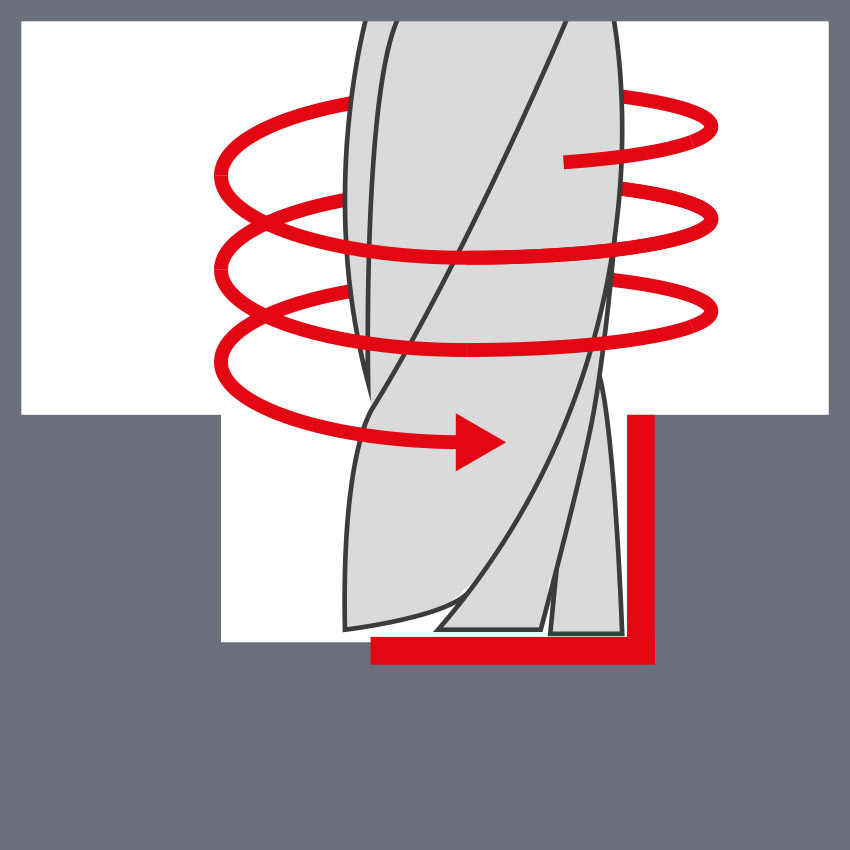
Eintauchen in der Helix
- Zustellung: 5-15% der Werkzeugdurchmessers pro programmierter Helix Bahn
Helix Bahn Durchmesser: ca. 1,7x dem Werkzeugdurchmesser
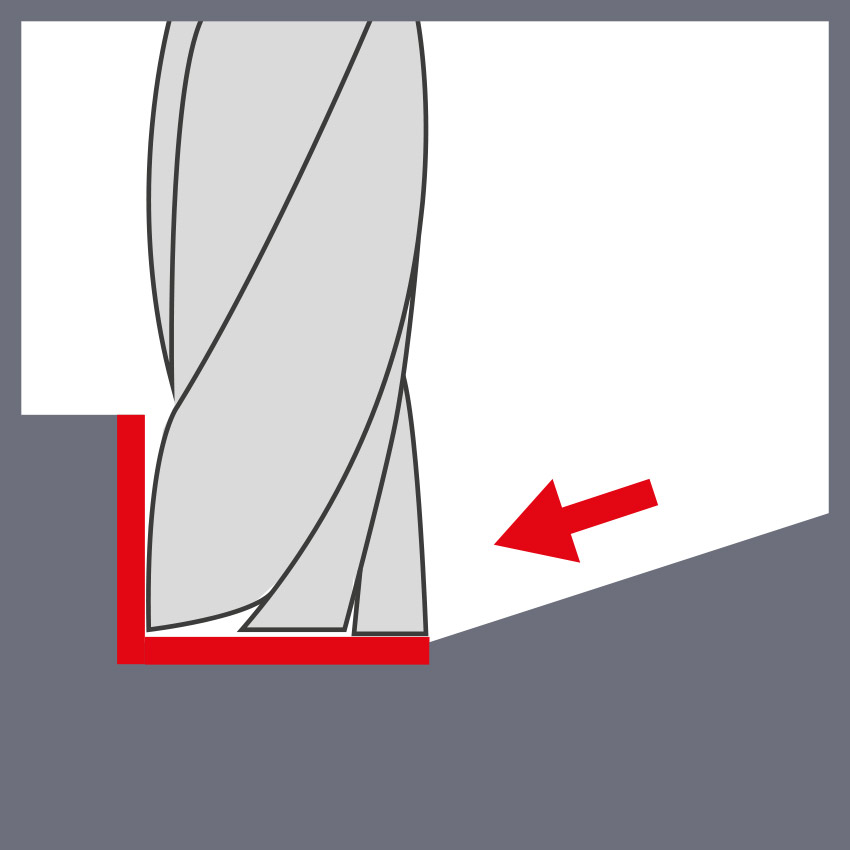
Eintauchen in der Rampe
- Rampenwinkel: 1°-4° (< Ø3 mm nur 0,5°)
Vorschubreduktion: ca. 50-75% des Vorschubes (Materialabhängig)
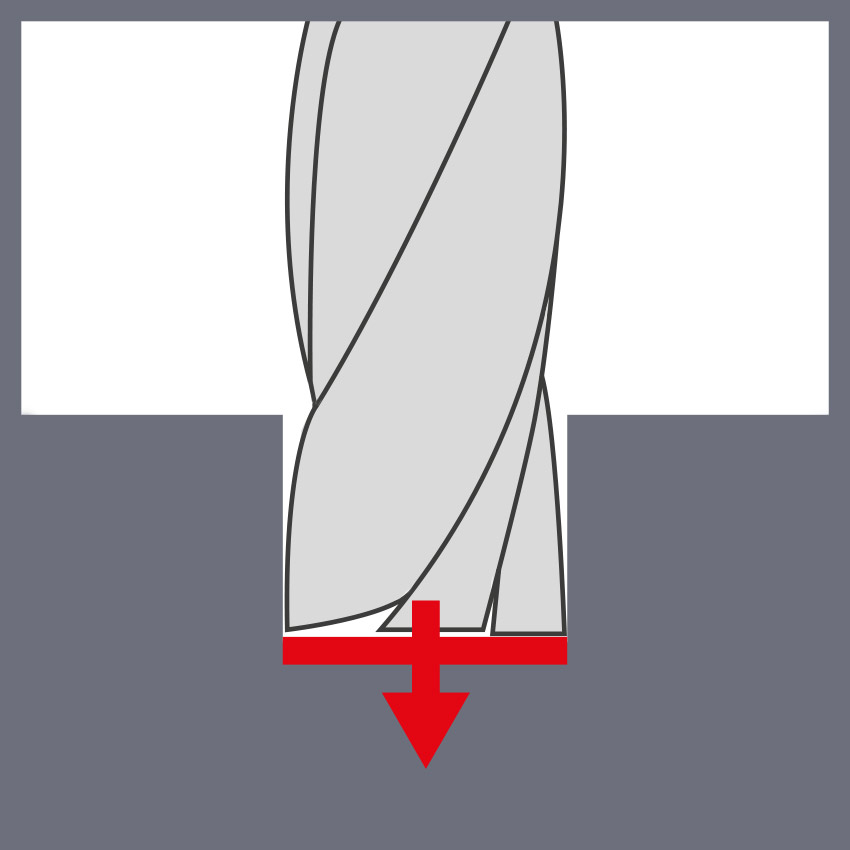
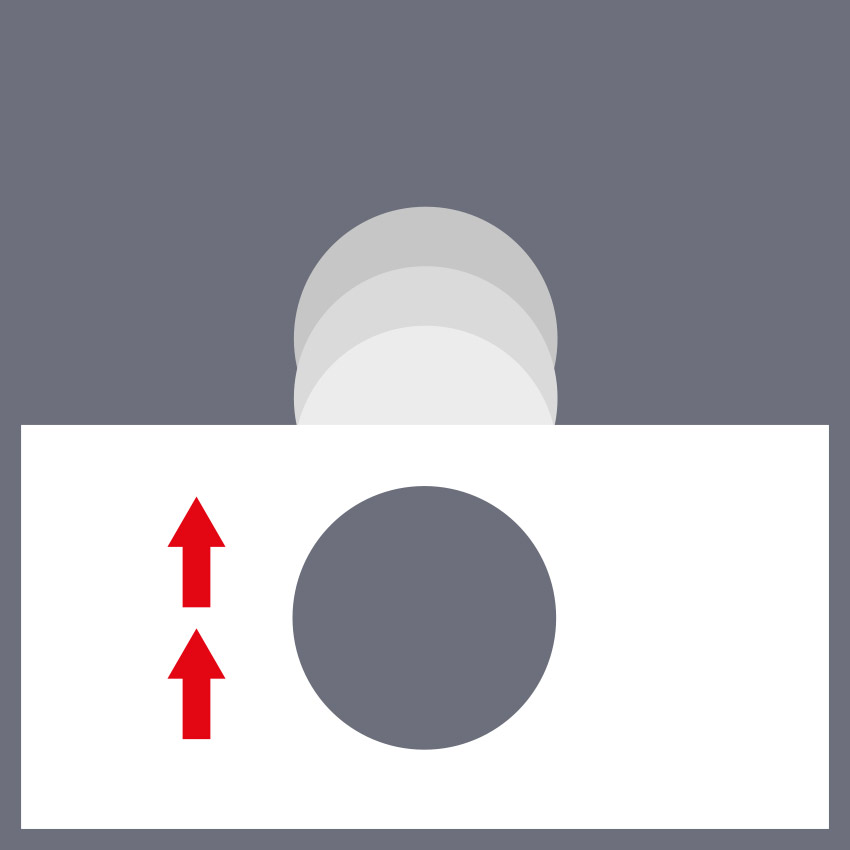
STECHEN
Seitliche Zustellung: Ca. 25% des Werkzeugdurchmessers
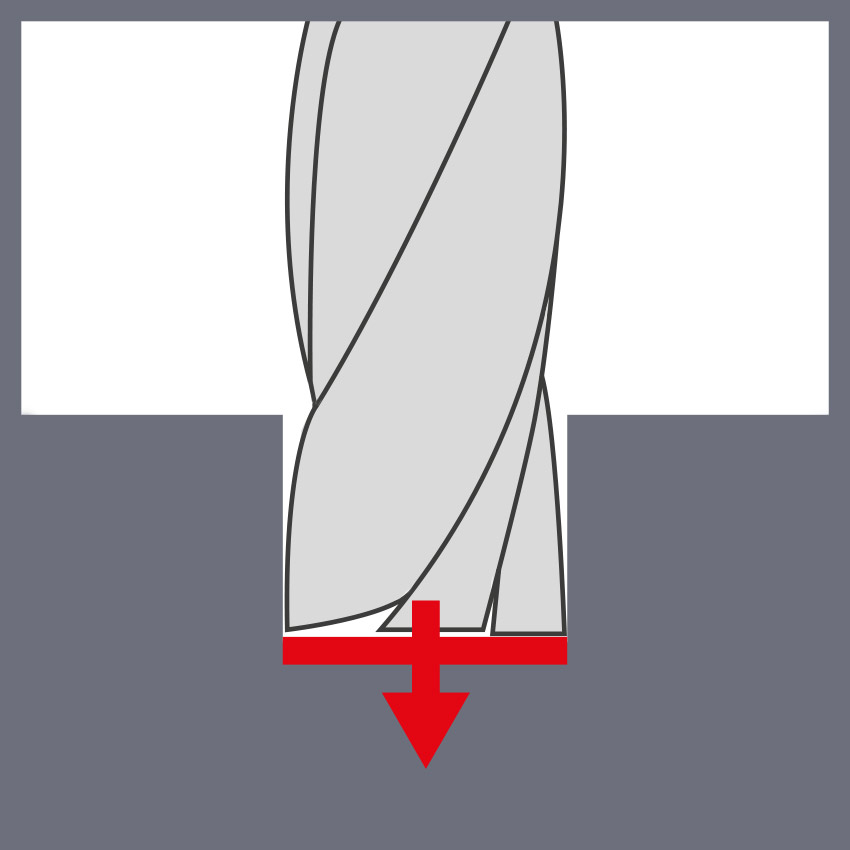
FÚRÁS
- Tiefe sollte nicht mehr als 0,5xD betragen > danach lüften
- Vorschub verringern auf fz=50%
Trochoidalfräsen
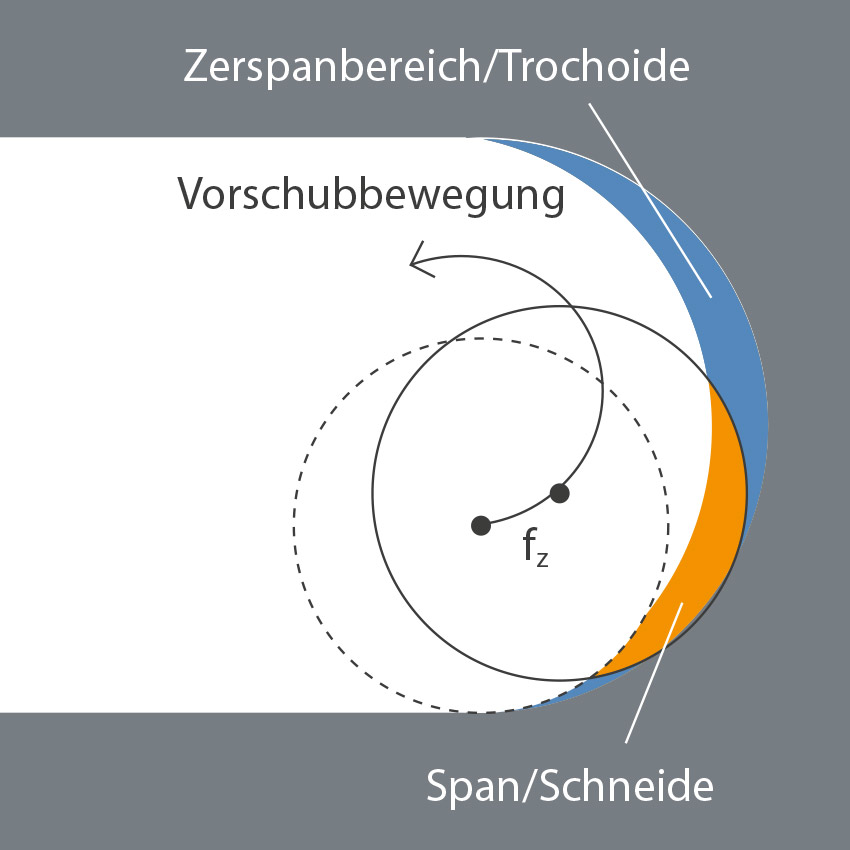
- 10-15% ae (seitliche Zustellung) vom Werkzeugdurchmesser
- Auf Vorschub achten, programmierter Vorschub soll eingehalten werden, ansonsten Reduktion der Vc (Drehzahl).
- Nutfräsen > Durchmesser mind. 20% – 25%
- Eintauchen mit Helix > Durchmesser x 2 – 10% – 15%
- Umschlingungswinkel max. 60%
Online-Rechner
- Allgemeine Formel Formenbau:
(Fräser Ø/100)* Z x F x Drehzahl → Vorschub
Wert FW = Schruppen 3 (max. 4) / Schlichten 2,5 (max. 3)
- Zähnezahl beachten / ist das Werkzeug angestellt oder nicht.
- Auf max. Drehzahl der Maschine achten.
Zustellungen bis Ø6 - ap= ca. 6% vom Werkzeugdurchmesser
- ae= ca. 16% vom Werkzeugdurchmesser
Online Rechner
Umfangfräsen (allg. Stahl) ae=10-30%, ap=2-2,5xD
fz = Ø3-Ø6 > 1,3% vom Werkzeugdurchmesser
fz = Ø7-Ø12 > 0,9% vom Werkzeugdurchmesser
fz = Ø13-Ø20 > 0,8% vom Werkzeugdurchmesser
fz rostfrei > -12% von Stahl
Vollnutfräsen (allg. Stahl) ae=100%, ap=1xD
fz = Ø3-Ø6 > 0,8% vom Werkzeugdurchmesser
fz = Ø7-Ø12 > 0,6% vom Werkzeugdurchmesser
fz = Ø13-Ø20 > 0,5% vom Werkzeugdurchmesser
fz rostfrei > -25% von Stahl
Schnittgeschwindigkeit Richtwerte
WERKSTOFF | VOLLNUTFRÄSEN [m/min] | UMFANGFRÄSEN [m/min] | KOPIERFRÄSEN [m/min] |
---|---|---|---|
P K | 90 | 140 | 150 |
M | 50 | 80 | 75 |
S | 40 | 60 | 60 |
N | 300 | 500 | 600 |
P
K | M | S | N | |
Vollnutfräsen m/min | 90 | 50 | 40 | 300 |
Umfangfräsen m/min | 140 | 80 | 60 | 500 |
Kopierfräsen m/min | 150 | 75 | 60 | 600 |
hm-Wert als entscheidender Faktor
Ø | P | H | M | N | S |
2 | 0,01 | 0,01 | 0,01 | 0,01 | 0,01 |
3 | 0,015 | 0,012 | 0,015 | 0,02 | 0,015 |
4 | 0,025 | 0,02 | 0,015 | 0,025 | 0,015 |
5 | 0,035 | 0,025 | 0,03 | 0,04 | 0,025 |
6 | 0,035 | 0,025 | 0,03 | 0,05 | 0,025 |
8 | 0,04 | 0,03 | 0,035 | 0,05 | 0,03 |
10 | 0,05 | 0,035 | 0,04 | 0,06 | 0,035 |
12 | 0,055 | 0,035 | 0,045 | 0,07 | 0,04 |
16 | 0,065 | 0,04 | 0,055 | 0,07 | 0,05 |
20 | 0,065 | 0,04 | 0,055 | 0,08 | 0,05 |
Berechnung Vorschub/Zahn
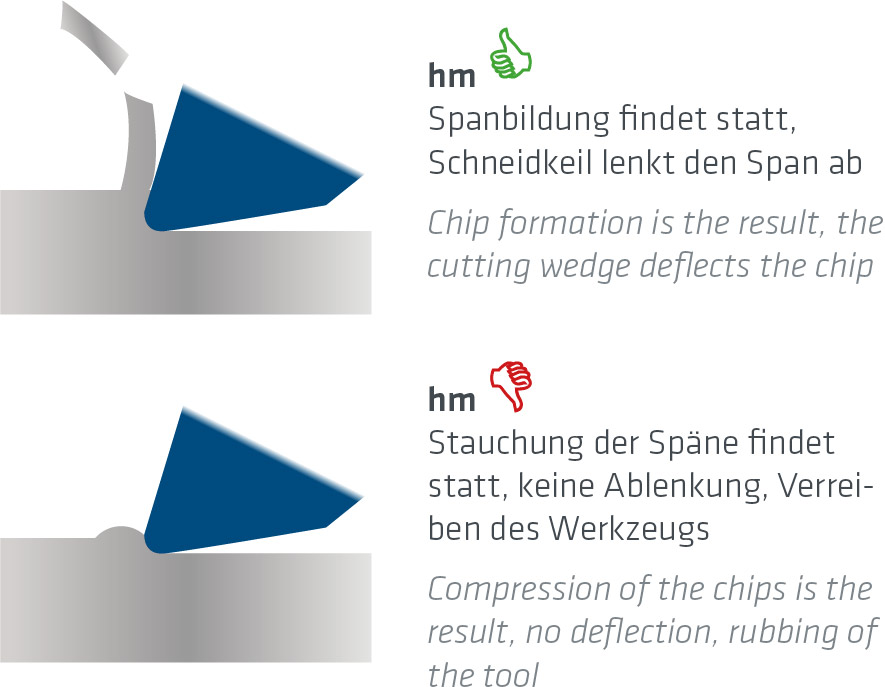
Ø | P | H | M | N | S |
2 | 0,01 | 0,01 | 0,01 | 0,01 | 0,01 |
3 | 0,015 | 0,012 | 0,015 | 0,02 | 0,015 |
4 | 0,025 | 0,02 | 0,015 | 0,025 | 0,015 |
5 | 0,035 | 0,025 | 0,03 | 0,04 | 0,025 |
6 | 0,035 | 0,025 | 0,03 | 0,05 | 0,025 |
8 | 0,04 | 0,03 | 0,035 | 0,05 | 0,03 |
10 | 0,05 | 0,035 | 0,04 | 0,06 | 0,035 |
12 | 0,055 | 0,035 | 0,045 | 0,07 | 0,04 |
16 | 0,065 | 0,04 | 0,055 | 0,07 | 0,05 |
20 | 0,065 | 0,04 | 0,055 | 0,08 | 0,05 |
Tipps gegen übermäßigen Verschleiß
Verschleißart
Maßnahmen
Freiflächenverschleiß
Abnutzung zwischen Werkstück und Freifläche
- Schnittgeschwindigkeit verringern (Vc)
- Vorschub erhöhen (fz)
- Kühlmitteldruck erhöhen


Freiflächenverschleiß
Abnutzung zwischen Werkstück und Freifläche
Maßnahmen:
- Schnittgeschwindigkeit verringern (Vc)
- Vorschub erhöhen (fz)
- Kühlmitteldruck erhöhen

Aufbauschneide
Material bleibt durch Aufschweißung auf der Schneidkante haften
- Schnittgeschwindigkeit erhöhen (Vc)
- Vorschub verringern (fz)
- Kühlmitteldruck erhöhen
- Werkzeug mit schärferer Schneide


Aufbauschneide
Material bleibt durch Aufschweißung auf der Schneidkante haften
Maßnahmen:
- Schnittgeschwindigkeit erhöhen (Vc)
- Vorschub verringern (fz)
- Kühlmitteldruck erhöhen
- Werkzeug mit schärferer Schneide

Ausbrüche entlang der Schneidkante
entstehen durch Vibrationen, Spänestau, Kammrisse und zu hohe Sprödigkeit des Werkstoffes
- Schnittgeschwindigkeit verringern (Vc)
- Vorschub erhöhen (fz)
- Kühlmitteldruck erhöhen
- Werkzeug mit Kantenpräparation z.B. VSO einsetzen


Ausbrüche entlang der Schneidkante
entstehen durch Vibrationen, Spänestau, Kammrisse und zu hohe Sprödigkeit des Werkstoffes
Maßnahmen:
- Schnittgeschwindigkeit verringern (Vc)
- Vorschub erhöhen (fz)
- Kühlmitteldruck erhöhen
- Werkzeug mit Kantenpräparation z.B. VSO einsetzen

Plastische Verformung
durch zu hohe Temperaturen bzw. bei zu hoher mechanischer Beanspruchung
- Schnittgeschwindigkeit verringern (Vc)
- Vorschub verringern (fz)
- Kühlmitteldruck erhöhen


Plastische Verformung
durch zu hohe Temperaturen bzw. bei zu hoher mechanischer Beanspruchung
Maßnahmen:
- Schnittgeschwindigkeit verringern (Vc)
- Vorschub verringern (fz)
- Kühlmitteldruck erhöhen
